隔离用户及敏感电子部件是电机控制系统的重要考虑事项。安全隔离用于保护用户免受有害电压影响,功能隔离则专门用来保护设备和器件。
电机控制系统可能包含各种各样的隔离器件,例如:驱动电路中的隔离式栅极驱动器;检测电路中的隔离式ADC、放大器和传感器;以及通信电路中的隔离式SPI、RS-485、标准数字隔离器。无论是出于安全原因,还是为了优化性能,都要求精心选择这些器件。
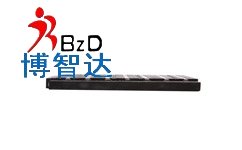
虽然隔离是很重要的系统考虑,但它也存在缺点:会提高功耗,跨过隔离栅传输数据会产生延迟,而且会增加系统成本。系统设计师传统上求助于光隔离方案,多年来,它是系统隔离的最佳选择。
最近十年来,基于磁性(变压器传输)方法的数字隔离器提供了一种可行且在很多时候更优越的替代方案;从系统角度考虑,它还具备系统设计师可能尚未认识到的优点。接下来介绍两种隔离解决方案,重点论述磁隔离对延迟时序性能的改善,以及由此给电机控制应用在系统层面带来的好处。
隔离方法
光耦利用光作为主要传输方法,如图1所示。发送侧包括一个LED,高电平信号开启LED,低电平信号关闭LED。接收侧利用光电检测器将接收到的光信号转换回电信号。隔离由LED与光电检测器之间的塑封材料提供,但也可利用额外的隔离层(通常基于聚合物)予以增强。
图1. 光耦结构
光耦的最大缺点之一是:LED老化,会使传输特性漂移;设计人员必须考虑这一额外问题。LED老化导致时序性能随着时间和温度而漂移。因此,信号传输和上升/下降时间会受影响,使设计复杂化,尤其是考虑到本文后面要处理的问题。
光耦的性能扩展也是受限的。为了提高数据速率,必须克服光耦固有的寄生电容问题,该问题会导致功耗升高。寄生电容还会提供耦合机制,导致基于光耦的隔离器件的CMTI(共模瞬变抗扰度)性能劣于竞争方案。
磁隔离器(基于变压器)已大规模应用十多年,是光耦合器的有效替代方案。这类隔离器基于标准CMOS技术,采用磁传输原理,隔离层由聚酰亚胺或二氧化硅构成,如图2所示。低电平电流以脉冲方式通过线圈传输,产生一个磁场,磁场穿过隔离栅,在隔离栅另一侧的第二线圈中感生一个电流。由于采用标准CMOS结构,其在功耗和速度方面具有明显优势,而且不存在光耦合器相关的寿命偏差问题。此外,基于变压器的隔离器的CMTI性能优于基于光耦合器的隔离器。
图2. 磁性变压器结构
基于变压器的隔离器还允许使用常规的信号处理模块(防止传输杂散输入)和高级传输编解码机制。这样就可以实现双向数据传输,使用不同编码方案来优化功耗与传输速率的关系,以及将重要信号更快速、更一致地传输到隔离栅另一端。
延迟特性比较
所有隔离器的一个重要但常常被轻视的特性是其传输延迟。此特性衡量信号(可以是驱动信号或故障检测信号)沿任一方向跨过隔离栅所需的时间。技术不同,传输延迟差别很大。通常提供的是典型延迟值,但系统设计师特别关注最大延迟,它是设计电机控制系统需要考虑的重要特性。表1给出了光耦合器和磁隔离栅极驱动器的传输延迟和延迟偏差值示例。
表1: 光耦合器和磁隔离器的典型延迟特性
如表1所示,磁隔离在最大延迟和延迟可重复性(偏差)方面优势明显。这样,电机控制设计人员对设计将更有信心,无需增加时序裕量以满足栅极驱动器特性。对于电机控制系统的性能和安全,这都有着非常重要的意义。
对电机控制系统的系统影响
图3显示了交流电机控制应用中采用的典型三相逆变器。该逆变器由直流母线供电,直流电源通常是通过二极管桥式整流器和容性/感性-容性滤波器直接从交流电源产生。在大部分工业应用中,直流母线电压在300 V至1000 V范围内。采用脉宽调制(PWM)方案,以5 kHz至10 kHz的典型频率切换功率晶体管T1至T6,从而在电机端子上产生可变电压、可变频率的三相正弦交流电压。
图3. 电机控制应用中的三相逆变器
PWM信号(如PWMaH和PWMaL)在电机控制器(一般用处理器和/或FPGA实现)中产生。这些信号一般是低压信号,与处理器共地。为了正确开启和关闭功率晶体管,逻辑电平信号的电压电平和电流驱动能力必须被放大,另外还必须进行电平转换,从而以相关功率晶体管发射极为接地基准。根据处理器在系统中的位置,这些信号可能还需要安全绝缘。
栅极驱动器(如图3中的GDRVaL和GDRVaH)执行这种功能。每个栅极驱动器IC都需要一个以处理器地为基准的原边电源电压和一个以晶体管发射极为基准的副边电源。副边电源的电压电平必须能够开启功率晶体管(通常为15 V),并有足够的电流驱动能力来给晶体管栅极充电和放电。
逆变器死区时间
功率晶体管有一个有限的开关时间,因此,上桥和下桥晶体管之间的脉宽调制波形中必须插入一个死区时间,如图4所示。这是为了防止两个晶体管意外同时接通,引起高压直流母线短路,进而造成系统故障和/或损坏风险。死区时间的长度由两个因素决定:晶体管开关时间和栅极驱动器传输延迟失配(包括失配的任何漂移)。换言之,死区时间必须考虑PWM信号从处理器到上桥和下桥栅极驱动器之间的晶体管栅极的任何传输时间差异。
图4. 死区时间插补
死区时间会影响施加到电机的平均电压,尤其是在低速运转时。实际上,死区时间会带来以下近似恒定幅度的误差电压:
其中,VERROR为误差电压,tDEAD为死区时间,tON和tOFF为晶体管开启和关闭延迟时间,TS为PWM开关周期,VDC为直流母线电压,VSAT为功率晶体管的导通状态压降,VD为二极管导通电压。
当一个相电流改变方向时,误差电压改变极性,因此,当线路电流过零时,电机线间电压发生阶跃变化。这会引起正弦基波电压的谐波,进而在电机中产生谐波电流。对于开环驱动采用的较大低阻抗电机,这是一个特别重要的问题,因为谐波电流可能很大,导致低速振动、扭矩纹波和谐波加热。
在以下条件下,死区时间对电机输出电压失真的影响最严重:
高直流母线电压
长死区时间
高开关频率
低速工作,特别是在控制算法未添加任何补偿的开环驱动中
低速工作很重要,因为正是在这种模式下,施加的电机电压在任何情况下都非常低,死区时间导致的误差电压可能是所施加电机电压的很大一部分。此外,误差电压导致的扭曲抖动的影响更有害,因为对系统惯性的滤波只有在较高速度下才可用。
在所有这些参数中,死区时间长度是唯一受隔离式栅极驱动器技术影响的参数。死区时间长度的一部分是由功率晶体管的开关延迟时间决定的,但其余部分与传播延迟失配有关。在这方面,光隔离器显然不如磁隔离技术。
应用示例
为了说明死区时间对电机电流失真的影响,下面给出了基于三相逆变的开环电机驱动的结果。
逆变器栅极驱动器采用ADI公司的磁隔离器 (ADuM4223ADuM4223),直接驱动IR的IRG7PH46UDPBF1200VIGBT,直流母线电压为700V,逆变器驱动开环V/f控制模式下的三相感应电机。利用阻性分压器和分流电阻,并结合隔离式∑–∆调制器(同样是来自ADI公司的AD7403),分别测量线电压和相电流。各调制器输出的单位数据流被送至控制处理器 (ADI公司的ADSP-CM408) 的sinc滤波器,数据在其中进行滤波和抽取后,产生电压和电流信号的精确表示。
sinc数字滤波器输出的线电压实测结果如图5所示。实际线电压为10kHz的高开关频率波形,但它被数字滤波器滤除,以便显示我们感兴趣的低频部分。相应的电机相电流如图6 所示。
图5. 实测线间电机电压:(左)500 ns死区时间;(右)1 µs死区时间
图6. 实测电机电流:(左)500 ns死区时间;(右)1µs死区时间
ADuM4223栅极驱动器的传输延迟失配为12ns,因此可以使用IGBT开关所需的绝对最短死区时间。对于IRIGBT,最短死区时间可设置为500ns。从左图可看出,这种情况下的电压失真极小。同样,相电流也是很好的正弦波,因此扭矩纹波极小。右图显示死区时间提高到1µs时的线电压和相电流。此值更能代表光耦合栅极驱动器的需求,因为其传播延迟失配和漂移更大。电压和电流的失真均有明显增加。这种情况使用的感应电机是相对较小的高阻抗电机。
在更高功率的终端应用中,感应电机阻抗通常要低得多,导致电机电流失真和扭矩纹波增加。扭矩纹波在很多应用中都会产生有害影响,例如:电梯乘坐舒适度下降或机械系统中的轴承/联轴器磨损。
过流关断
现代栅极驱动器的另一个重要问题是处理器发出的关断命令能以多快的速度在IGBT上实现。这对于以下情况中的过流关断很重要:过流检测不是栅极驱动器本身的一部分,而是作为检测与滤波电路的一部分加以实现。这方面的另一个压力是更高效率IGBT的短路耐受时间缩短。对此,IGBT技术的趋势是从业界标准10µs缩短到5µs甚至更短。如图7所示,过流检测电路通常需要数微秒时间来锁存故障;为了顺应总体发展趋势,必须采取措施来缩短这一检测时间。该路径中的另一主要因素是从处理器/FPGA输出到IGBT栅极(栅极驱动器)的传播延迟。
同样,磁隔离器相对于光学器件有明显优势,原因是前者的传播延迟值非常小,通常在50ns左右,不再是影响因素。相比之下,光耦合器的传播延迟在500ns左右,占到总时序预算的很大一部分。
图7. 故障关断时序
电机控制应用的栅极驱动器关断时序如图8所示,其中处理器的关断命令跟在IGBT栅极发射极信号之后。从关断信号开始到IGBT栅极驱动信号接近0的总延迟仅有72 ns。
图8. 过流关断栅极驱动器时序
小结
随着人们更加关注系统性能、效率和安全,电机控制架构师在设计稳健系统时面临着日益复杂的挑战。基于光耦合器的栅极驱动器是传统选择,但基于变压器的解决方案不仅在功耗、速度、时间稳定性上更具优势,而且如本文所述,由于信号延迟缩短,其在系统性能和安全方面也有明显优势。这使得设计人员可以在防止上桥和下桥开关同时接通的同时,有把握地缩短死区时间,改善系统性能。
此外,它还支持对系统命令和错误作出更快速的响应,这同样能增强系统可靠性并提高安全性。鉴于这些优势,基于变压器的隔离式栅极驱动器已成为电机控制系统设计的一个主要选择;强烈建议系统设计人员在设计下一个项目时,把器件延迟作为一项重要要求。